Getting Started
Login, Modules Overview, and Access
Analytics Overview
Support Options
Billing Module
Flourish Supported Hardware, Networking, and Vendors
Edit Your Flourish Software User Profile
Submit a New Idea to Flourish Software
Configuration & Setup
Company Settings
Editing Your Company Profile
Automatically Lock Packages Based on Test Result Status
Upload Your Company Logo
Facility Settings
Creating Locations and Areas
Facility Tag Settings
Manage Facility Payment Methods
Facility Compliance Screen
Update License Number
Update Phone Number
Configure and Manage a Reverse Sync User
Configurations per Facility
Labels & Printing
Flourish Label Maker - Configure Labels
Understanding Label Configuration Settings
Flourish Label Selection & Capabilities
How to Add a Reference Field to a Label
Printer and hardware options and setup
QZ Tray Certificate renewal
Flourish Software Cannabinoid and Terpene List
Flourish COA Portal QR Code - Arizona Requirements
Distribution
Distribution Setup
Managing Destinations
Create and Update Destinations In Bulk
Managing Sales Reps
Assign Sales Reps to a Destination
Add/Create Vendors
Create And Update Vendors In Bulk
How to Tag Drivers
Create and Manage Vehicles
Create And Manage Drivers
Users & Permissions
User Roles and Facility Permissions
Creating and Managing Users
Setting Up Users for Mobile Access
How to enable "Update financial info for shipped orders"
Enable Add a New Physician to User Roles
Resetting Your Password in Flourish
Reset User PIN (Point of Sale or Mobile)
Retail POS - Allow to Allocate Inventory to a Purchase Order Manually
Prevent Users from Exporting All Grid Data
Manufacturing Machine & Run Configuration
Bulk Item Price Updates - Item Pricing
Create and Update Strains in Bulk
Enable the creation of new items from the Inventory Screens
Update Items in bulk
Cultivation
Grow / Cultivation Overview
Entering in Dry Weights
Overview: Plant Groups and Plant Batches
Change Strain on a Plant
How to split a group
Changing the UOM of a Harvest's Wet Weight
Creating "Fresh Frozen" packages - all you need to know
How to Bulk Destroy Plant IDs
Adjust Expected Harvest Date
Entering in Wet Weights by Individual Plant
Splitting Immature Plant Groups
Non-METRC Creating a Package of Clones
Manicure Harvest
How to create strains
How to Move Plants
How to Create Clones From a Mother Group
Entering in Wet Weights by Group (non-METRC)
METRC Harvest: Record Wet Weight with Scale and Scanner
Cultivation Area Attributes
How to Manicure a Harvest
Creating New Strains
Entering in Dry Weights and Creating Packages from Harvest
How to Apply Additives to Plants
How to Kill plants
Recording Waste for Harvests (METRC)
Destroying Plants: Logging Waste / Notes
Cultivation - How to Revive Plants (No Tracking System)
Creating Plants Overview
Move harvested strains back to the Flowering phase
Record METRC Harvest with Total Wet Weight
Reprint Plant Tags
Making "Fresh Frozen" products from a Harvest in the "Processing" stage.
Non-METRC - Move a harvest back from 'Processing' to the 'Harvest' phase
How to Kill Individual Plant IDs
How to Make a Mother Group
Kill Individual Plant IDs from Plant Groups
NON-METRC - How to Make a Clone
Harvest packages and Configuration
Making "Fresh Frozen" products from wet weights.
Canada - Destroy plants
METRC Harvesting - wet and dry weights, waste, harvest packages and completion.
Complete and Uncomplete a Harvest
Creating a Package from Harvest
Flourish Analytics
Flourish Analytics - Getting Started
Flourish Analytics - Set User Access and Access Level
Flourish Analytics - Browse Content
Flourish Analytics - Set a Workbook as Favorite
Flourish Analytics - Customize and Bookmark the Data
Flourish Analytics - Export Data
Flourish Software messages and notifications
Android Mobile App
Mobile App: General
Flourish Android Mobile App Overview
Mobile App Login
Mobile User Roles
Mobile Scanning Devices
Mobile Zebra Scanners - connect to Flourish Software app - DataWedge App Setup
Android App Mobile Settings: Choose Package ID to Display
Mobile App: Cultivation
Mobile App - Using a scanner for Cultivation Actions
Mobile App - Harvest - Scan and Record Weights for Plants
Mobile App: Inventory
Mobile App Inventory: Assign a Package to an Order
Mobile App Inventory: Update Lot Number for Non-Cannabis Inventory
Mobile App Inventory: Locate Non-Cannabis
Mobile App Inventory: Take Lab Sample
Mobile App Inventory: Create a New Package
Mobile App Inventory: Lock Package
Mobile App Inventory: Adjust Package
Mobile App Inventory: Adjust Non-Cannabis Inventory
Mobile App Inventory: Locate Package
Mobile App: Inventory Counts
Mobile Inventory Counts Overview
Mobile Inventory Count - Enter the Number of Packages per Item
Mobile Inventory Counts: Scan Packages per Item
Mobile App: Outbound
Mobile App: Shipments
Android mobile - Allocate non-cannabis inventory
Mobile Order Line Screen
Mobile App: Build Orders by Scanning and Allocating Packages
Mobile App: Retail
eCommerce
Jane Technologies
Flourish WooCommerce
Setting up WordPress Site, WooCommerce, and Plugins
Flourish WooCommerce Wholesale Configuration Guide
WooCommerce Wholesale Store Branding and Client Experience Guide
Managing Multi Accounts and Sub Accounts in WooCommerce
Flourish Wholesale Portal User Guide for Buyers
Order Sync Workflow - WooCommerce to Flourish Application
Inbound
Inbound Module Overview
Inbound Purchase Orders
Inbound - Display Additional fields next to item names on purchase order lines
Tutorial: Create Purchase Order
Receive Inbound Transfers and Purchase Orders (No Compliance System)
Inbound - Receive The Whole Purchase Order In One Click
Quick Receive Non-Cannabis Inventory
Moisture Tracking
METRC Inbound Process
Inventory
Bulk Actions
Bulk Actions - Add Packages to an Order
Bulk Actions - Combine Packages
Bulk Actions - Locate Packages
Bulk Actions - Lock and Unlock Packages
Bulk Actions - Add to a Manufacturing Run
Bulk Actions - Print Package Labels
Bulk actions - Update Unit weight
Create Items in Bulk
Inventory Counts
Inventory Settings
Item Creation & Management
Package Unit Cost Inheritance and Calculation
Creating a Custom Category
Manage Item Ecommerce Names
Add Ingredients to Items and print in outbound PDF
Rename Areas
Inventory Management Principles
Classes & Categories
Disabling Areas
Clone an Existing Item or BOM
Lock Codes, Adjustment Codes, & Return Reasons
External and Internal Items
Item Tagging Functionality
Clone an Item to Create A New Item
Chart of Account Mapping
Configuring Item E-Commerce Categories and Subcategories
Item Strain Type
Inventory Management
Custom Grid Column Ordering
Brand Management
Web Inventory Counts: Enter the Number of Packages per Item
Print Labels For Non-Cannabis Items
Tutorial: Creating an Item
Create Package from Package
Inventory Adjustments
Create And Manage Custom Views
Managing Inventory Lock Codes
Managing Chart of Accounts View - QuickBooks Online
Package History
Create Lab Samples when a Lab Test Batch "Required Testing" (LTB Option) is required.
Create multiple packages with different quantities in one session.
Update The Unit Weight for a single package
Create or edit a Brand for an Item.
Reprint Package Label
Automatically calculate the "Use By Date" for new packages.
Inventory: Recording a lab result and uploading COAs
Non-Inventory Items
METRC - Creating Trade Sample Packages and Trade Sample Adjustments
Inventory: Package Reference Fields
Flourish Costing
Inventory Audits
METRC - Retag Packages - Change the item of a package.
Flourish Inventory
Editing Items after Creating Packages
METRC - Discontinue package in METRC and Re-sync to Flourish
Set The Unit Weight for Packages of Items with UOM of 'Each'
Refreshing Inventory Count Details
Outbound - Return Rejected Items to Inventory
MMJ Used Package Attribute
Manage Packages waste
Managing Non-Cannabis Inventory
Creating Packages and Auto-Prompting Label Printing
Inherit Package Attributes
Add or Edit the Harvest Date for a Package
Inventory: Upload PDF To Record Lab Test Results
Refresh Inventory of Non-Cannabis Items
Inventory: Package Attributes
Manufacturing
Manufacturing Module Overview
Manufacturing Work Orders with BOMs
Creating Bill of Materials for Handling Case Quantities
Manufacturing Waste Log
Creating a Bill of Materials - BOM
Start a New Manufacturing Run
Creating Inventory using Bill of Materials
Outbound
Outbound Overview
Outbound Invoice
Outbound orders Payment Status
Outbound Order Discounts and Charges
Creating New Outbound Shipments (Non-METRC)
Add, Edit and Delete Order Notes
Scan Packages to add Order Lines and Allocate Packages to Outbound Orders
Allocate Packages to Outbound Order
Sales Order Approval
Outbound Order Notes
Outbound Module Operational Overview
Invoice Date
Split Packages During Order Allocation
Display Unit Cost and Total Cost when allocating packages to an outbound order.
Creating New Outbound Orders
Configuration: Only Show Items with Available Quantity
Allocate Packages to an Outbound Order
Find Orders
Set a Default Distributor for your Outbound orders
Un-Ship a Shipment
Change Facility - Move an Outbound Order between Flourish Facilities.
New York - Outbound - Manage Adult-Use Cannabis Products Tax
Printing Options on a Sales Order
Selling Cannabis Inventory by Lot
California Excise Tax Rate 2023 Update
How to update financial info for shipped orders
Packing List
Outbound Order Status Fields
Mark Sales orders as fully paid
Sales Order Payments
Retail / POS
AeroPay
POSaBIT
Customer Management
Adding a Physician
Creating a Customer Profile
Merging Customer Profiles
Customer Preferred Name
Edit the credit available to customers
In-Store, Delivery, and Pickup Orders
Retail POS Printing and Reprinting Receipts
Retail Purchase Limit Enforcement
Creating a Retail Delivery Route
Retail POS Printing Customer Labels
Customer Deliveries (Non-METRC)
Checking In a Customer
METRC Retail Delivery: Edit order after marking “Out For Delivery”
Create Retail Pick Up and Delivery Orders
Retail Order Statuses
Retail POS Refund a Purchase
Fulfilling a Retail Order
POS Item Scanning Rules
Retail POS Complete a Purchase
Retail POS Create an In-Store Purchase
Retail - POS - Split an order line into multiple lines of the same item.
Removing an Order from the POS
Retail POS - Refund a Manual Card Transaction
Retail POS - Refund a POSaBIT - Manual Transaction
Retail POS Quick Sale
Retail - Med and Rec purchases
Retail POS - Refund an AeroPay Transaction
Replace Customer - Change the Customer on a Retail Purchase
Retail - Cancel a Completed Purchase
Till and Vault Management
Creating a Retail Transfer
Creating a Sub-Vault
Performing Pay Ins and Pay Outs
Closing a Till
Counting a Vault
Opening a Till
Reconciling E-Payments
Creating Retail Reasons
Creating a Till
Integrations
MMUR
MMUR CureAPI v4 (Florida Only)
MMUR Caregiver Selection
Florida Retail - Automatic Dispensation to MMUR on Delivery Orders
MMUR / CureAPI v4 Medical Cannabis Aggregate Limit
Alpine IQ Integration
Discounts
Retail Discounts Overview
Creating a Retail Discount
Retail — Standard and Advanced Discounts
Retail Discounts — Customer Attributes
Retail Discounts — Order Attributes
Applying a Retail Discount
Common Retail Discounts
In Store Menu
Flourish Software In Store Menu
In Store Menu Eligibility: Items and Discounts
In-Store Menu Controls
Vector Payments
Vector Payments Configuration
Vector Payments - POS Check Out and Reporting
Troubleshooting Vector Payments Terminals Not Connecting
Retail
Till Report
Recording a POSaBIT transaction
Retail - POS - Set default printers and print
Retail Pre-Orders, Backorders, and Replacement Orders
Adding Payment Terminals & Assigning to a Till
Retail Purchase limits
Retail - Customer State ID, Medical ID data and expiration
Retail - Mark a Completed Purchase as Cancelled
Point of Sale Cash Drawer Configuration
Retail - Show Tax Breakdown by Type on Retail Sales Receipt
Retail Facility Configuration
Credit Card Manual payments for Retail Point of Sale
Retail Metrc Sync Error "Package Cannot Be Sold Because it Doesn't Exist in The Current Facility"
Retail - Void a Transaction
Retail - Export the Customer Purchase History
BioTrack
BioTrack (Connecticut)
Connecticut BioTrack Inbound
Connecticut BioTrack Cultivation Guide
Connecticut BioTrack Manifest Requirements
Connecticut Manifesting in Flourish for BioTrack Clients
Connecticut BioTrack Inventory
Connecticut BioTrack Category Conversions
Connecticut BioTrack - Accepting Rejected Inventory
BioTrack (Florida)
Florida BioTrack Integration Overview
Florida BioTrack Limitations
Florida BioTrack User Management
Florida BioTrack Drivers and Vehicles
Florida BioTrack Inventory Categories and Mapping
Florida BioTrack Item MMUR Configuration
Florida BioTrack Propagation
Florida BioTrack Cultivation Management
Florida BioTrack Harvesting
Florida BioTrack Inventory Creation
Florida BioTrack Inventory Destruction
Florida BioTrack Inventory Adjustments
Florida BioTrack - Undo Out of Sync Package
Florida BioTrack Inventory Count
Florida BioTrack Initial Inventory During 90 Day Conversion Window
Florida BioTrack Delivery Devices
Florida BioTrack Facility Areas Creation
Florida BioTrack Lab Samples and COA Management
Florida BioTrack Manufacturing
Florida BioTrack: Report Ingredients During Manufacturing
Florida BioTrack Inbound Receiving and Transfers
Florida BioTrack Order Fulfillment and Shipping
Florida Biotrack Retail Returns, Restocks, and Voids
Florida BioTrack: Plant Additives
Florida BioTrack: Retail POS User Guide
Florida BioTrack: Retail Fulfillment User Guide
Florida BioTrack: Retail Delivery User Guide
BioTrack (New York)
BioTrack New York Go-Live Steps
New York BioTrack Integration Overview
New York BioTrack Limitations
New York BioTrack User Management
New York BioTrack Facility Areas Creation
New York BioTrack Drivers and Vehicles
New York BioTrack Inventory Categories and Mapping
New York BioTrack Propagation (Create Plants)
New York BioTrack Cultivation Management
New York BioTrack: Plant Additives
New York BioTrack Harvesting
New York BioTrack Inventory Creation
New York BioTrack Inventory Destruction
New York BioTrack Inventory Adjustments
New York BioTrack Inventory Count
New York BioTrack - Undo Out of Sync Package
New York BioTrack Initial Inventory During 30 Day Conversion Window
New York BioTrack Lab Samples and COA Management
New York BioTrack Manufacturing
New York BioTrack: Create Initial Inventory
New York BioTrack Receiving Transfers
New York BioTrack Order Fulfillment and Shipping
New York BioTrack Retail Returns, Restocks, and Voids
New York BioTrack: Retail Delivery User Guide
New York BioTrack Inventory Transfers to Destination Not On BioTrack
External API
Flourish Webhooks
Securing your webhooks
Flourish Software External API Key Management
Generate or Reset External API key
Integrations
Apex Trading
BarTender™
Google Workspace
LeafLink
LeafLink Integration Overview
LeafLink Integration Setup
Flourish LeafLink Integration Setup DIY - Start here!
Before Setting Up LeafLink Integration
LeafLink Integration Setup and Activation
After Setting Up and Activating the LeafLink Integration
Set a default Sales Representative for a customer in Leaflink
Leaflink Category Mapping with Custom Categories
Sync Flourish to multiple Leaflink Companies and Brands
LeafLink - Sell by Batch
LeafLink Integration - Exclude facilities from inventory quantity sync
Set The Status of Leaflink Orders to Sync To Flourish Software.
Leaflink Brands and Product Lines
LeafLink Troubleshooting
Outfield
Ordo
POSaBIT POS
QuickBooks Online
What Version of QuickBooks Online is Supported?
Integration: QuickBooks Online
QuickBooks Online Sync Settings
Enable Shipping Charges in QuickBooks Online
Disconnect (Un-map) Items, Destinations and Vendors
Setting Inventory Start Date
Switch your QuickBooks Online Account to work with Categories
Enable Syncing of Outbound Orders to Quickbooks
Transition an Item from "Inventory" to "Non-Inventory" types in Flourish and QBO.
Quickbooks Online: Syncing Order Discounts
Send Flourish Data To QBO Sales Order Custom Fields
Zapier
Seed Technology Integration
Export Data From Flourish To QuickBooks Desktop
CYBRA MarkMagic® Integration Setup
Lendica Integration
Flourish Analytics – Green Check Integration and Verified Reports
METRC
METRC CA Microbusinesses Location Functionality.
Step 1 - preparing for METRC CA Location Functionality for Microbusinesses.
Step 2 - preparing for METRC CA Location Functionality for Microbusinesses.
My Package is out of sync - Location Invalid
Step 3 - Locate your packages - METRC CA Location Functionality for Microbusinesses
Location Functionality for California Microbusinesses
METRC Integration Overview
How to find or generate your METRC API key
Sync cultivation Data from METRC
METRC -Handle Out Of Sync Package, Item, Plant, Harvest or Strain.
My item is out of sync - How to get it back in sync with METRC
METRC - Assigning Tags to Plants & Packages
METRC - Killing mature plants - additional details
METRC - Creating clones overview
California METRC cultivators - How to create clones from immature plants batches.
METRC - Handling rejected outbound packages
Managing Your Compliance System Credentials Flourish
2. Differences in METRC and non-METRC installations of Flourish Software
METRC MO, OH and MA - include or exclude the prefix in names of items synced from METRC.
METRC - Inbound a package and use it to create clones
Manage METRC Tags
Creating Outbound Shipments and METRC Transfers
METRC Item Brands
METRC - Undo Package - Remove a created package that is out of sync
METRC CA - Edit cultivation tax on Inbound Orders
METRC - Create a Transfer Template
How to Resync a package
Sync an Item from METRC
Retry sync - a case of invalid tag
METRC "External Transfer" - bring cannabis items into the METRC ecosystem.
Flourish Manufacturing Run Sync As METRC Processing Job
METRC – "Replace Tag" for Plants and Plant Batches
METRC - Get my plants back in sync
Import METRC Categories
Un-map Out of Sync Items
Retry Sync after the issue was resolved
METRC - Rename a Harvest
Auto-assign tags to items created by METRC reverse sync
METRC - My Retail Order is Out Of Sync
METRC CA - Reducing Immature Plant Batches - additional details
METRC Harvest - Retry Harvest Sync
METRC - Out of Sync Strain
Retry Sync - Case of "User not Authorized"
Un-sync An Item From a METRC Facility - Delete a Mapping Record
My package is out of sync
METRC – Change Strain for Plants and Plant Batches
METRC - Get my clone batch back in sync
Release Notes
Previous Release Notes
2020.02.23 - Software Release 4.6.0
2020.03.23 - Software Release 4.8.0
2020.04.06 - Software Release 4.9.0
2020.04.20 Software Release 4.10.0
2020.04.13 - Software Release 4.9.2
2020.05.04 Software Release 4.11
2020.05.18 Software Release 4.12.0
2020.06.01 Software Release 4.13.0
2020.06.15 Software Release 4.14.0
2020.06.22 Software Release 4.14.1
2020.06.29 Software Release 4.15.0
2020.07.13 Software Release 4.16.0
2020.07.27 Software Release 4.17.0
2020.08.10 Software Release 4.18.0
2020.09.02 Software Release 4.19.0
2020.09.14 Software Release 4.20.0
2020.09.28 Software Release 4.21.0
2020.10.12 Software Release 4.22.0
2020.10.26 Software Release 4.23.0
2020.11.09 Software Release 4.24.0
2020.11.30 Software Release 4.25.0
2020.12.14 Software Release 4.26.0
2020.12.29 Software Release 4.26.1
2021.01.11 Software Release 4.28.0
2021.01.25 Software Release 4.29.0
2021.02.09 Software Release 4.30.0
2021.02.25 Software Release 4.31.0
2021.03.09 Software Release 4.32.0
2021.03.23 Software Release 4.33.0
2021.04.09 Software Release 4.34.0
2021.04.21 Software Release 4.35.0
2021.05.03 Software Release 4.36.0
2021.05.18 Software Release 4.37.0
2021.06.08 Software Release 4.38.0
2021.06.29 Software Release 4.39.0
2021.07.20 Software Release 4.40.0
2021.08.03 Software Release 4.41.0
2021.08.17 Software Release 4.42.0
2021.08.31 Software Release 4.43.0
2021.10.05 Software Release 4.45.0
2021.10.19 Software Release 4.46.0
2021.11.02 Software Release 4.47.0
2021.11.16 Software Release 4.48.0
2021.11.30 Software Release 4.49.0
2021.12.14 Software Release 4.50.0
2021.12.28 Software Release 4.51.0
2022.01.11 Software Release 4.52.0
2022.01.25 Software Release 4.53.0
2022.02.08 Software Release 4.54.0
2022.02.22 Software Release 4.55.0
2022.03.08 Software Release 4.56.0
2022.03.22 Software Release 4.57.0
2022.04.05 Software Release 4.58.0
2022.04.19 Software Release 4.59.0
2022.05.03 Software Release 4.60.0
2022.05.17 Software Release 4.61.0
2022.06.01 Software Release 4.62.0
2022.06.14 Software Release 4.63.0
2022.06.28 Software Release 4.64.0
2022.07.12 Software Release 4.65.0
2022.07.26 Software Release 4.66.0
2022.10.18 Software Release 4.72.0
2022.12.13 Software Release 4.76.0
2022.11.15 Software Release 4.74.0
2022.12.28 Software Release 4.77.0
2022.08.23 Software Release 4.68.0
2022.10.04 Software Release 4.71.0
2022.08.09 Software Release 4.67.0
2022.11.1 Software Release 4.73.0
2022.09.07 Software Release 4.69.0
2022.11.29 Software Release 4.75.0
2022.09.20 Software Release 4.70.0
2024.05.30 Software Release 4.106.0
2024.01.23 Software Release 4.100.0
2024.03.26 Software Release 4.103.0
2023.10.17 Software Release 4.96.0
2023.09.06 Software Release 4.94.0
2023.08.08 Software Release 4.92.0
2025.06.24 Software Release 4.119.0
2024.02.13 Software Release 4.101.0
2023.05.02 Software Release 4.85.0
2023.01.24 Software Release 4.79.0
2023.05.16 Software Release 4.86.0
2023.11.28 Software Release 4.98.0
2023.06.13 Software Release 4.88.0
2023.03.21 Software Release 4.83.0
2023.07.25 Software Release 4.91.0
2023.04.04 Software Release 4.84.0
2023.06.27 Software Release 4.89.0
2023.11.06 Software Release 4.97.0
2024.06.26 Software Release 4.107.0
2025.04.01 Software Release 4.114.1
2024.08.20 Software Release 4.109.2
2025.04.23 Software Release 4.116.0
2023.02.21 Software Release 4.81.0
2023.06.01 Software Release 4.87.0
2025.05.13 Software Release 4.117.0
2024.09.10 Software Release 4.111.0
2023.07.11 Software Release 4.90.0
2024.03.05 Software Release 4.102.0
2023.01.10 Software Release 4.78.0
2023.12.17 Software Release 4.99.0
2025.03.11 Software Release 4.114.0
2024.11.20 Software Release 4.112.0
2023.03.07 Software Release 4.82.0
2024.05.07 Software Release 4.105.0
2023.09.26 Software Release 4.95.0
2023.08.22 Software Release 4.93.0
2023.02.07 Software Release 4.80.0
2025.06.03 Software Release 4.118.0
2024.04.16 Software Release 4.104.0
2025.08.04 Software Release 4.120.0
- All Categories
- Inventory
- Inventory Management
Inventory Management
The Inventory Module allows you to organize all Cannabis and Non-Cannabis inventory, run inventory counts and audit logs, & lock and unlock specific items. METRC sync available. Inventory Module Navi…
The Inventory Module allows you to organize all Cannabis and Non-Cannabis inventory, run inventory counts and audit logs, & lock and unlock specific items. METRC sync available.
Inventory Module Navigation

# | Description |
1 | Dropdown menu of Actions for Inventory Items
|
2 | Submodules |
3 | Filter view columns |
4 | Export data to Excel |
Terms to Know
Inventory Count module uses the following terms:
Term | Definition |
Assigned | Items that are Assigned or packed in bags for Pickup or Delivery orders. In Flourish, these items are also Unlocked. |
Available | Items that are available for sale. In Flourish they are referred to as Unlocked. The physical boxes have been opened and items are available for sale. Flourish updates the Inventory module with the Available value when the count is Completed. |
Not Available | Items that are Not Available for sale. In Flourish they are referred to as Locked. The physical boxes remain closed until items are ready for sale. |
The Inventory module serves many purposes, but basically boils down to two main functions.
- Reviewing, reporting or monitoring your current inventory of both cannabis and non-cannabis items.
- Creating new inventory by using three different options; From Packages; From Blended Oils and From Bill of Materials.
Navigating On Hand Inventory
The default view when you first enter the Inventory screen is your current listing of available cannabis inventory. We have also added a search bar to easily, search items by Package ID, SKU Name or Item Name. This data set can be sorted and filtered by one of the many columns of attributes regarding your inventory. At any point when you have your all packages data sorted, filtered and sub-filtered you can export to a Comma-Separated Values file (".CSV") at any time.
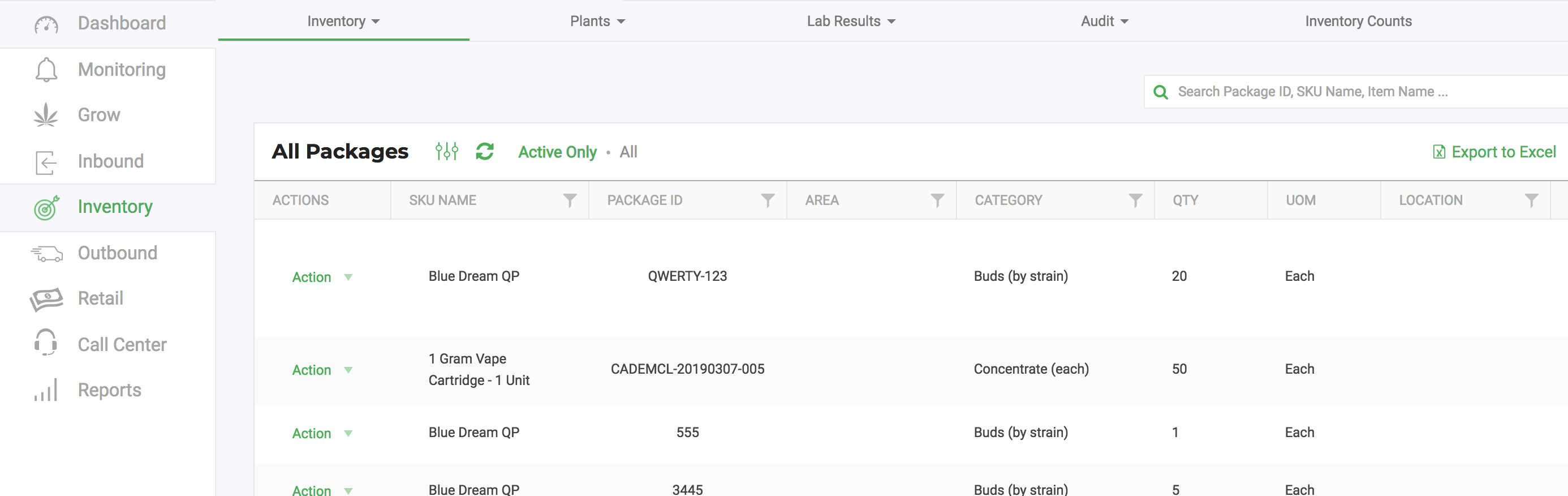
By using the green equalizer widget next to "All Packages", a user can custom sort the columns in whichever order they prefer and turn any of them off if they don't need to be used.
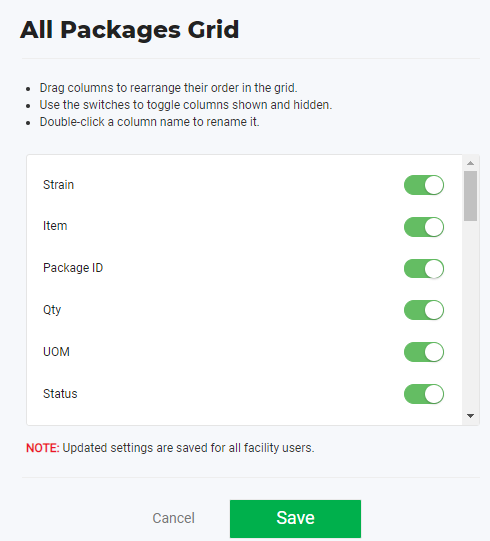
Creating Inventory
Creating inventory is one of the main components of the Flourish Software platform. There are three ways to create inventory in Flourish:
- From Packages – When you create inventory From Packages you can do one of two things; break larger packages down into smaller packages and create new source packages. The From Packages screen has two initial steps a review and then a final confirmation.Typically, four high-level processes are involved in creating inventory from packages:
- Select the Item of the new inventory you are about to create or breakdown. Then select the strain if the item is strain specific, the numbers of packages and the weight or quantity of each package.
- The second step is to select the source package from which you are removing inventory from in order to create the new packages. You select from a drop-down list (sorted by FIFO – Oldest package is listed first) or you can search by the last four digits of the package. Once you have the correct package selected you can click buttons to consumer the entire amount of the source package or only the required quantity based on the number of packages x quantity per package in step 1.
- Review – This is on the same screen as steps one and two and is asking you to review the quantities that you are creating and consuming. If there is a variance in the case of extraction or production, you will need to acknowledge the differential and can choose to have the differential deposited into the Waste Log. If you have the state tracking system integration turned on (e.g. - METRC), here is where you will select the next sequence of new packages tags that will be assigned to the newly created packages and automatically reported back to the state system.
- Confirm New Packages – This is the final step to creating new packages of inventory. On this screen you can fill out or add the following data points for this transaction:
- Created Time/Date Stamp
- Area/Location of where the new packages will be located
- LOT/Batch # - Assign your own internal batch or lot number
- Reference Notes – free form notes for instructions for this package
- Processing Duration – Time captured if this was an extraction or production
- Temperature – same as above
- Pressure – same as above
- Equipment Code – log the machine or equipment used to make these packages
- Ref Field 2 – Open-ended note (e.g. Person's initials who weighed the cannabis or actually operated the equipment)
- Ref Field 3 – same as above

- From Blending Oils – Users can select their item, number of packages and quantity per package. You can also select up to two source packages and add their appropriate quantities to blend which will create a new package. The system will automatically calculate the appropriate quantity of each package based on percentages of THC/CBD of each package and the desired results. (e.g. 2 to 1 ratio THC to CBD) After selecting a tag number, you can review and confirm. To view your newly created item, you can select "All Inventory" from the Inventory Submodule.
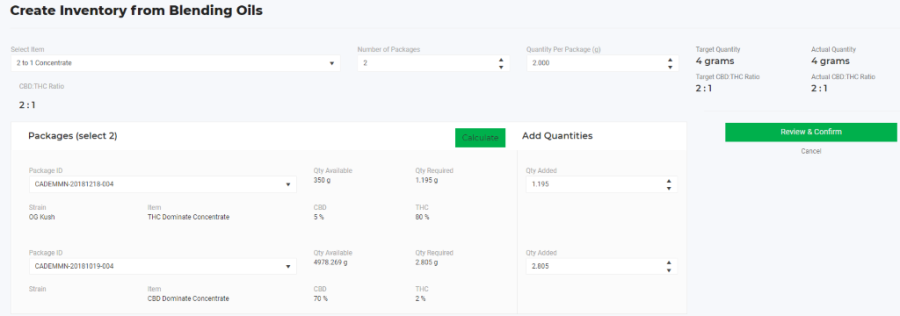
- From Bill of Materials – Users can select the item, strain, number and quantity along with bill of materials for creating new packages. Once all of the base line criteria has been entered, the BOM components will show (see below) the expected amount to be consumed, the amount you actually have on hand. If any of your components don't have sufficient levels of inventory the system will not let you process and put any items into a negative count. Finally, users can edit the allocation quantity of the components for that item. After selecting a tag number, you can review and confirm. To view your newly created item, you can select "All Inventory" from the Inventory Submodule.
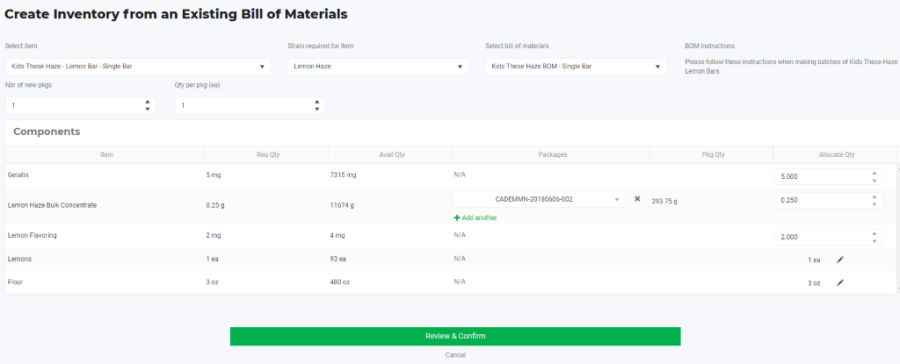
Confirmation Screen – Just like the From Packages option, when creating your new packages using the Bill of Materials you will also get a final Confirmation screen where you can enter:
- Created Time/Date Stamp
- Area/Location of where the new packages will be located
- LOT/Batch # – Assign your own internal batch or lot number
- Reference Notes – free form notes for instructions for this package
- Processing Duration – Time captured if this was an extraction or production
- Temperature – same as above
- Pressure – same as above
- Equipment Code – log the machine or equipment used to make these packages
- Ref Field 2 – Open-ended note (e.g. Person's initials who weighed the cannabis or actually operated the equipment)
- Ref Field 3 – same as above
Newly Created Packages
Now that you have created some new packages in inventory using one of the three options above, your next option might be to take a small quantity from the package and create a new package that can be for Lab Testing, Trade Samples and Internal QC Samples.
Lab Samples - From the Action drop-down menu next to the package, select Create Lab Sample. This will open the same screen as From Packages. Here is will ask you to verify the number of packages and quantity of each package that will be sent out for lab testing.After you have created your new lab sample, the best practice is to lock the package, so it doesn't accidentally end up in an Outbound Sales Order or as part of new package creation before the testing results come back. When you lock the package, you can select from a list of reason codes for the lock. In this case we would want one in the system called Quarantine. (Reason codes for inventory locking can be created by going to Manage Settings > Inventory > Items > Inventory Lock Codes). Once the lab results have been returned, they can be recorded by selecting Record a Lab Result on the Action drop down menu next to the original package (not the lab sample)If the lab results come back positive, you can unlock the original package by selecting "unlock" from Action drop-down menu of the applicable package.
Trade and QC Samples – These two samples are created by using the Adjust Quantify option from the Action drop down menu next to your package. After you adjust what you want the new quantity to be, the software will make the calculation for you and then you can select from a drop-down list of Reason Codes, two of which are Trade and QC samples.
Managing Inventory
Users can manage inventory through the Inventory Counts Submodule within the Inventory Module.Inventory Counts allows the user to view a snapshot of the following information:
- Total packages/counted
- Total Non-Cannabis lines/lines counted
- Total discrepancies
Package-specific information as well:
- SKU Name
- Package ID
- Expected QTY
- Actual QTY
- Adjustment codes
- Notes
Package History
Package history can be easily viewed within your Inventory module.

Click any package to view it's history

Quickly navigate between Ancestry or Descendants
Export the package history to Excel
Managing Waste
Users can manage their waste through the waste log functionality which can be found under the Inventory Submodule dropdown. Once in the Waste Log a user can choose to dispose of the waste for tracking or compliance reasons.Users can export all data to Excel

Inventory Counts
Inventory counts are a best practice, and often a regulatory requirement. Flourish provides the following method to conduct an inventory count.
Tips:
- Inventory counts currently are done on a "Frozen" manner, thus it is recommended to count when there is no inventory movement
- You do not have to do a full physical count. If the user doesn't enter a value in the Counted Quantity, the item or package will be marked as not counted.
Workflow:
- Navigate to the Inventory > Inventory Counts screen
- If you have permissions enabled (generally manager level), click "Start Count)
- At this point the count freezes a snapshot of the current on hand inventory
- Users will fill in the counted quantity for each package or item
- Available Quantity is active inventory
- Non-Available Quantity is any quantity that is locked or assigned to a purchase
- Once complete, move the count to Pending status and save
- A manager can then review the count and make any adjustments if needed by selecting the adjustment code and entering a comment
- The count can then be moved to Complete status. At this time all adjustments are finalized and the count is complete
Inventory Adjustment
Inventory within Flourish can be adjusted using the Inventory module.
- First, select the facility where the inventory is located from the drop-down list at the top of the Flourish web app.

- Next, find the package you want to adjust and select the Action drop-down to its left.
- Choose Adjust Qty.
- Within the Adjust Quantity modal, you must first select an Adjustment Code Reason

- NOTE: Flourish has pre-configured adjustment codes available for users.
- Users can also create their own new adjustment codes as well.
- All adjustments can easily be edited or configured to meet the User's needs.
- Users can navigate to this functionality from the Inventory Module and Items sub-module within Manage Settings under User Profile.
- Next, enter the New Quantity in the middle-right section of the modal and notice the Quantity to Adjust field calculated for you.

- Add any relevant Comments and click Save.
- New package quantities will now be reflected in the Inventory module.
Lab Testing Results
Flourish provides a repository for all testing results. Test results can be associated to a Lot Number (Batch Code) or to a specific Package ID.
All Lab Results can be found in the Inventory Module > Lab Results Sub Module. Lab results tied to a package can also be linked to from the respective package.

To log a lab result, either choose "Record a lab result" from the Package Action Menu or navigate to Inventory > Lab Results and select the package and chose "Record a lab result" from the Actions button on the top right.

Elements:
- Required:
- Is Final Result for Source Pacakage - useful if you record multiple tests against a package. This is the default flag and the "official" lab result
- Record against a Lot Number or a Package ID
- Select the respective Lot Number or Package ID
- Choose the Lab from the list defined in the Laboratory Master in settings
- THC Content
- CBD Content
- Analyzed Date
- Pass/Fail/In Progress Status
- Optional
- Choose one or more Sample Package IDs to associate to the result
- Fill in additional CBD-A, CBD, THC-A, Pesticide Pass, Solvents Pass attributes (expanding these in 2019)
- Upload up to three PDFs from the lab
How did we do?
Custom Grid Column Ordering